How do you assess and control vibration impacting sensitive equipment?
Welcome to another edition of Frequently Asked Questions about Noise, Vibration, and Acoustics. In this series, we answer questions that we hear most often from clients or through inquiries via our website. My name is Brian Howe, a Senior acoustical consultant and Principal at HGC. Today’s question is: “How do you assess and control the effects of vibration on high-sensitivity equipment that are used in labs or industry?”
Welcome to another edition of Frequently Asked Questions about Noise, Vibration, and Acoustics. In this series, we answer questions that we hear most often from clients or through inquiries via our website. My name is Brian Howe, a Senior acoustical consultant and Principal at HGC. Today’s question is: “How do you assess and control vibration impacting sensitive instruments and equipment?”
Vibration can negatively impact sensitive processes and equipment, whether it’s caused by trains, machinery or even footfalls. The impact of vibration can cause distortions of imaging results from technologies like magnetic resonance imaging machines (MRIs) and scanning electron microscopes (SEMs). Vibration can also lead to production failures during sensitive precision manufacturing of microelectronic devices such as semiconductors and silicon wafer chips.
To address today’s question, I will be briefly going over some examples of vibration sensitive instrumentation and processes. I will also review typical vibration criteria, assessment methodologies, and finally, vibration mitigation strategies.
Vibration Sensitive Technology Systems Like MRIs & SEMs
There are many examples of vibration sensitive equipment. As mentioned earlier, SEM images can be distorted by the impact of vibration. In the case of magnetic resonance imaging machines whether in hospitals or for test samples in laboratories, vibration impact is a little bit more complicated because MRI images are produced through a mathematical function so, unlike with SEMs, there’s no linear relationship between vibration and distortion. Ultrafine lithography in the semiconductor industry is another good example of a sensitive process that can be affected by vibration. Lithography produces patterns on wafer chips, and the impact of vibration can distort these patterns to the point where the chips are rendered unusable.
Criteria for Assessing the impact of Vibration on Sensitive Equipment
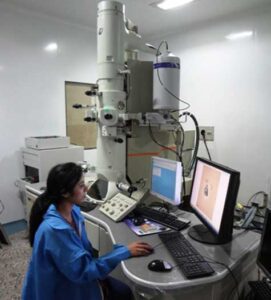
Several criteria can be used for assessing vibration on sensitive equipment. Generally, they follow an amplitude of the vibration, whether in displacement, velocity, or acceleration as a function of frequency in units of cycles per second, or hertz. The stringency of the vibration criteria is often related to the cost of the process. For example, distortion of a scanning electron microscope image caused by the impact of a nearby passing train may be easy to redo after a short time. However, with an automated process, such as DNA sequencing there’s no easy redo Even minor vibrations can have destructive consequences. Of course, there are other medical procedures in healthcare environments that are also highly sensitive to vibration, such as eye surgery, due to the use of surgical microscopes.
The most reliable vibration criteria normally come from the equipment manufacturer and are developed through either testing or field experience. Often there are vibration amplifications of certain components in a system. For example, the amplification of an arm supporting a surgical microscope eyepiece or the stylus of a Coordinate Measuring Machine (CMM). The manufacturers typically introduce damping and other measures to control these amplifications. But nonetheless, the vibration criteria can be more sensitive at those frequencies.
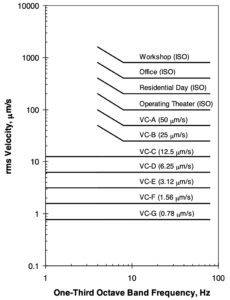
Generic Vibration Criteria
Generic vibration criteria started to be developed in the 1960s in the aircraft industry and has since gone on to be refined for other laboratory and electronic industries. Now commonly known as Vibration Criterion (VC) curves, going from VC-A and VC-B, all the way up to VC-G limits, which are in practice difficult to achieve. These vibration criteria have now been referenced in ISO standards, and in the design guidelines for the Canadian and American Institutes of Steel Construction.
Assessing Vibration using Seismic Accelerometers and Real-Time Frequency Analyzers
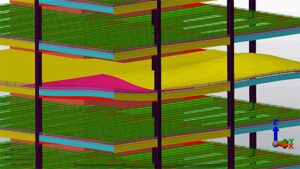
The most common method for assessing vibration is through measurements using seismic accelerometers and real-time frequency analyzers. The data is often used by itself or as input to a finite element analysis (FEA) program. FEA is a mathematical methodology that’s able to predict the response of a structure to effects of vibration as well as explore possible vibration mitigation options. Once a potential vibration issue is identified, mitigation needs to be considered, usually starting with the structural foundation or the machinery itself. For example, large concrete spread footings at the foundation can reduce vibration. So can large concrete caissons, particularly if you can get those caissons to extend down to bedrock. Other structural modifications can be achieved through added mass, stiffer beams, or vibration damping techniques.
Vibration Isolation Mounts for Sensitive Equipment
There are a host of vibration isolation mounts for supporting sensitive equipment. As a rule, the performance of a mount increases as the static deflection of that mount increases. For high-frequency vibration, rubber or polyurethane pads may be sufficient for mitigation. In cases where high/low frequency attenuation is required, steel or air springs are generally recommended. Very flexible systems, however, are not without drawbacks. Issues can result from the impact of an instrument operator accidently bumping his equipment, or vibration suddenly developing within a machine, such as a high-speed CMM. In these cases, it’s important to have an adequate concrete or steel inertia base for the machine and/or damping.
Passive vs Active Vibration Isolation Systems
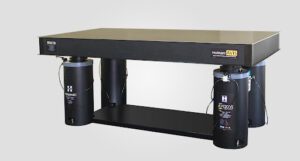
When passive isolation systems prove insufficient, consideration is then given to active vibration control systems, whereby sensors, as well as electric, pneumatic or hydraulic actuators (controlled by a processor) counter the vibration. Although more expensive than passive isolation systems, these active systems can control both the vibration feeding into the instrument from outside, and vibration produced by the machine itself.
In Conclusion
In conclusion, to help ensure the high performance of vibration sensitive instruments, it is important to assess and control vibration. It really is a complex matter to deal with and we’ve tried to present some of highlights of possible mitigation approaches in this post. If you have any further questions on this topic or have other questions you’d like to see answered, please feel free to reach out to me.